The Generalised
Process
- WVO pre-treatment
(filtration through 1mm2 filter).
This stage is vital as it removes any waste
food products that may be in the vegetable oil, it is also
useful to remove any excess water that may be in the oil at this
stage.
- Mix with catalyst (NaOH)
and ethanol.
The amount of alcohol is fairly fixed
throughout all processes; the amount of catalyst depends upon
the alcohol used, the catalyst used and the oil used in the
procedure. See the experimental section of this website for
further details.
- Reaction (transesterification).
Transesterification is the process of exchanging the alkoxy
group of an ester compound by another alcohol. These reactions
are often catalysed by the addition of an acid or base. It has been found that a vigorous stirring
at the initial stage is necessary to bring the oil, catalyst and
alcohol into intimate contact, however towards the end of the
reaction it can be beneficial to the reaction to decrease
mixing. Although it is advertised that heating is necessary at
the reaction process this is not specifically correct. Heating
during this process just speeds up the reaction as is shown in
the graph below (data from ‘Biodiesel Production Technology, J H
Van Gerpen, Biological and Agricultural Engineering, June 2006):
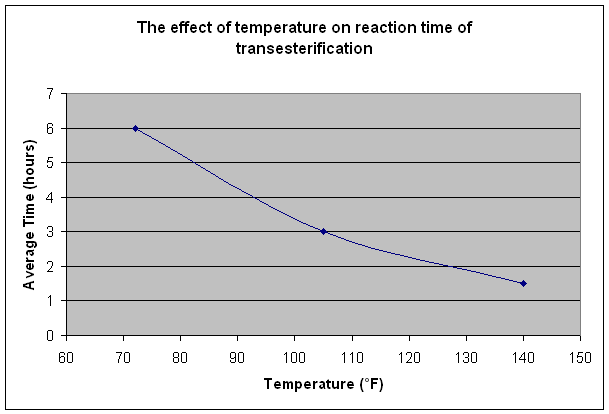
Although it may seem like a great idea to
increase the temperature so that the reaction takes less time
the boiling point of the alcohol has to be taken into account
(methanol ~65oC, ethanol ~78oC)
- Settling
This allows the glycerol, excess alcohol and
other waste products and impurities separate from the biodiesel.
The biodiesel will end up on top of the waste product.
- Separation (standards
for biodiesel only allow for ~0.24% glycerol to be present
in the end product)
The biodiesel has to be separated from the
glycerol by-product which can be further processed or disposed
of in the correct manor (see by-products section).
- Washing
The washing process is designed to purify the
biodiesel further. There are various procedures that can be
taken, bubble washing, mist washing and ‘dry’ washing are a few
examples. There are legal requirements that accompany washing
the product with water (see legal requirements section).
Most
of the impurities are in the glycerine, though there are still
small amounts of lye, soap, ethanol and water in the biodiesel,
which will cause trouble in your fuel system and engine. An easy
way to remove them is by washing the fuel with water. Add water
to the biodiesel until you have about 300ml of water to a litre
of biodiesel. The biodiesel floats on top of the water. As you
mix, the lye, soaps and ethanol are becoming dissolved in the
water, which makes it look cloudy. This is due to the fact that
water is better at dissolving the impurities than the biodiesel:
it is a more polar solvent. The mixing process needs to occur
carefully as the soap is an emulsifier and bounds the water and
the biodiesel when mixed violently. From the top the biodiesel
can be removed carefully and then the washing process can be
repeated. As more and more soap is removed from the biodiesel,
it becomes less able to bind water molecules, which means that
we are using water to dry the fuel.
After
the washing it is still necessary to give the fuel a final
filtration, it removes particles and traps of water. This can be
done with a J-cloth or a similar tightly-woven cloth. Normal
biodiesel has 1200-1500 ppm (parts per million) of water. Any
water above this level will damage your engine.
- Drying and
Filtering
As water is undesirable in the finished
product the biodiesel needs to be dried and filtered so that
only the purest biodiesel remains.
- Deal with
by-products (excess alcohol – recovery, glycerol, catalyst)
|