The design process chosen to be the most suitable for developing
countries uses the eight stages defined in "Procedures" Section
and is shown below.
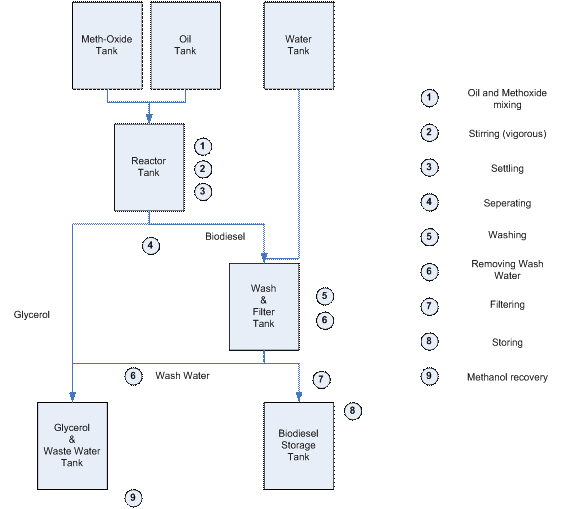
Many designs of biodiesel plant can be found in the market
currently, including both home and large scale production
biodiesel kits, with the majority of kits using one main tank
for reaction, settling, washing and separation. This is
considered space and cost saving, however does not allow for a
large production output due to the long time in which the
reaction tank is being used to settle the biodiesel.
To increase production rate we developed a “production-line”
style plant, with a module designed for each reaction stage,
which allows the slowest parts of the reaction to be
parallelised with identical modules, and faster processes
sharing equipment. This reduces wasted time with apparatus
unavailable or standing empty. It also allows the plant to start
small (basic kit) and grow over time by adding additional
modules, making it feasible as a project for a developing
country.
To make
it feasible to parallelise the plant, each module must be cheap,
which lead to the idea of using simple “off the shelf” parts,
then improving their effectiveness with clever design. Instead
of using an expensive conical settling tank, we will use a
simple drum, then have several taps up the side to allow the
biodiesel to be easily tapped off without mixing with the
by-product layer. Using simple, standardised and easy to source
parts makes maintenance easier, allowing the plant to remain in
operation for a long time.
Using gravity is the simplest way to have a non-automated plant
without requiring excessive manual labour. The cheapest and
safest way to implement this gravity feed system is to use a set
of different levels, created either with earth or a stand
system, ideally constructed with local recycled materials.
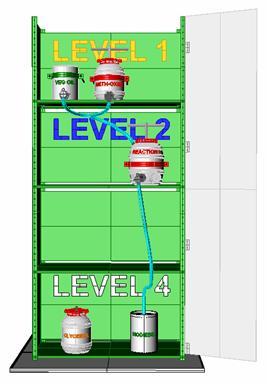 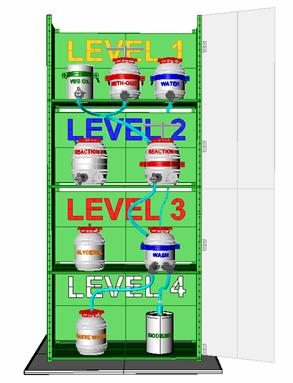
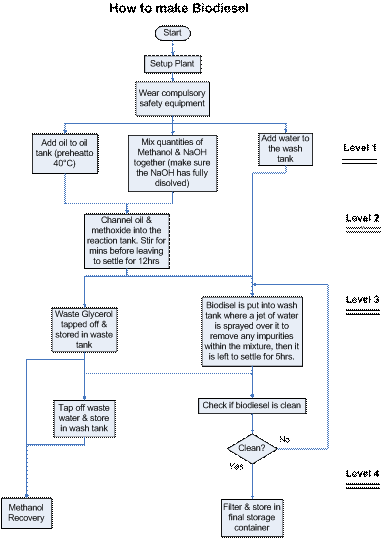
Using cheap modular
sections also allows the plant to start off small, minimising
start-up costs and operation complexity, which greatly increases
the chance that the plant will actually be used in rural
communities. When the operators are experienced and have
generated enough cash through biodiesel sales, more modules can
be bought to increase output. Biodiesel may even be used to
trade for local materials and supplies.
We are intentionally
designing the plant to be accommodating for future modifications
and additions, particularly for automation to be added. For
example an onsite diesel generator could power a pump to
transfer fluids and mix the meth-oxide and reaction tank.
However the plant layout is not the end product; ownership of
the plant within the rural area and education about the
biodiesel production process are essential to making an end
product which meets the specifications set by Vigyan Ashram.
Therefore it was decided to produce a “How To” Manual to explain
all processes, material choices and educate on safety aspects,
construction, and plant operation. This manual will also be
uploaded to a website to allow worldwide access to this
information.
It is our belief that such a simple plant design would be
readily accepted by developing countries, due to the ease of
start-up.
As the production of
biodiesel involves very reactive chemicals; methanol (a strong
solvent) and sodium hydroxide (extremely caustic), the choice of
materials is extremely important and crucial to the success of
the design.
Plain steel will corrode
rapidly and is therefore not an option. Stainless steel is
suitable but expensive and hard to work with, rendering it
impractical for even a UK kit, let alone for use in a developing
country. This leaves non-ferrous metals or polymers, with
polymers the most suitable option. It was decided to use PP
(Polypropylene) and HDPE (High Density Polyethylene) containers,
and PVC connection tubing, due to their high reaction
resistance.
Drums made of PP or HDPE are readily available from a multitude
of suppliers, which makes them cheaper than other polymer
containers, usually made to order.
The cost of setting up our biodiesel plant is
£345.18 for the Base and Safety kit. Addition modules which can
be added are a Washing and Methanol recovery kit. A full listing
of the costs involved can be found in "How To" Manual.
|
Plant
Modules |
Cost |
1 |
Basic Kit |
£230.27 |
2 |
Safety Kit |
£43.47 |
3 |
Washing Kit |
£42.07 |
4 |
Methanol Recovery Kit |
£29.37 |
|
Total |
£345.18 |
A prototype plant using the above concept design
was build and tested. A step- by- step instructuion can be found
in the "How To" Manual. The results of the produced
biodiesel are very promising.
|