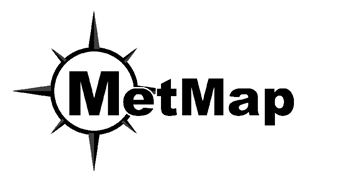
Integrated Metrology for Additive Manufacturing
17 July 2019, Advanced Manufacturing Training Centre
Airfield Drive, Ansty Business Park, Coventry, UK
Integrated metrology definitions
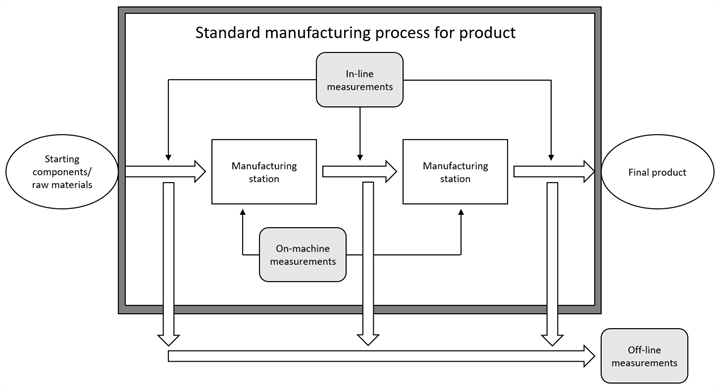
Figure 1. Flow diagram of a standard manufacturing process visually demonstrating where each type of integrated measurement takes place.
In-process
Any measurement taken that can be used to predict or detect issues during the manufacturing process. In-process measurements must be synchronised with the manufacturing process so that the process can be monitored. All in-process measurements must be integrated into the standard production process for the part being manufactured so that they are time sensitive. If a measurement is being performed during the manufacturing process, but is not being utilised for process monitoring and control, then that measurement is not in-process and is instead defined under off-line due to the purpose of the measurement.
Off-line
Any measurement that is not in-process. Off-line measurements are not synchronised with the standard manufacturing process and therefore cannot be used for process monitoring. A component measured off-line can be returned later to the process line but this measurement does not cause a time delay in the process of other components and is not an essential part of the production line. Off-line measurements will often be conducted outside of the manufacturing environment, either on a measurement station in the factory that is separate from the standard process line (sometimes referred to as at-line) or in a laboratory. Off-line measurements can also be in some cases on-machine, but never in-process, due to there not being an intent for process control with the data.
In-line
A form of in-process measurement that occurs right before, right after or between manufacturing stations. In-line measurements are taken on separate measurement systems along the standard production line where manufacturing is not occurring. These measurements are often taken off-machine, but in some situations may be on-machine if a single machine consists of several manufacturing stations. In-line measurements are regular and must be taken before the next stage of the process can continue, either for each individual part before it moves to the following manufacturing station, or as a sample from a batch. An in-line measurement must be part of the product’s standard manufacturing process and be used for process monitoring and control.
On-machine
A form of measurement that is used to record data on a station during manufacturing. On-machine measurements can determine any variable that provides information about the process. In many scenarios, on-machine measurements are in-process but can be off-line if the data is not being utilised for process monitoring and control. (In contrast, off-machine would describe any measurement that is not taken on the manufacturing station.)
In-situ
A form of on-machine measurement that primarily records data directly from the location where the manufacturing phenomenon is occurring. In-situ measurements are used to monitor how the equipment is interacting with the work piece. This can be through measuring at the point of interaction directly or through measurement of the work piece shortly after the phenomenon has passed, before the station’s task is complete.
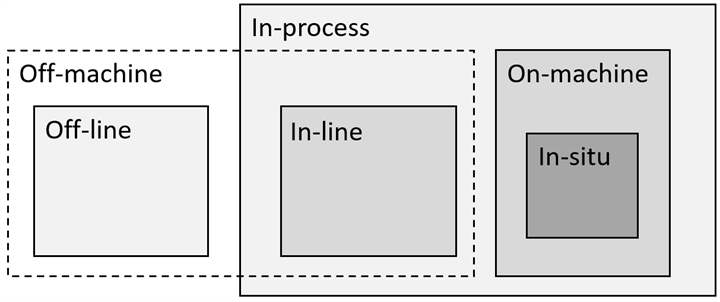
Figure 2. A demonstration of how the different metrological terms relate to each other in most circumstances. These terms can have some overlap, i.e. in-line and off-line measurements may be situated on-machine in some cases.
