Damage Modelling of Composites
Textile reinforcements are widely used in composite manufacturing in automotive sector. Predictive models which support a modern product development usually impose idealised meso-scale geometry on the textile reinforcements. However, composite manufacturing introduces defects into the structure of textile reinforcement making it irregular. This study aimed to implement a more realistic meso-scale model which included structural variability of the geometry (defects) in order to create better predictive models for mechanical properties of the composites. Case studies included analysis of 2D and 3D textile composites. Understanding of effect of the defects on mechanical properties will result in higher confidence of predictive modelling of composites.
Investigators:
Researcher:
- Twill weave laminate, carbon fibre/epoxy, volume fraction 55%
- Abaqus + periodic boundary conditions + UMAT subroutine
- Results predicted within 10% of experimental values
Experimental and predicted stress-strain curves
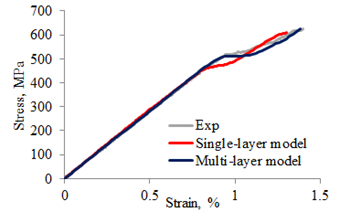
Damage progression in yarns transverse to loading direction (at strains 0.9%, 1% and 1.2%)
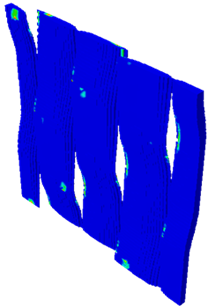
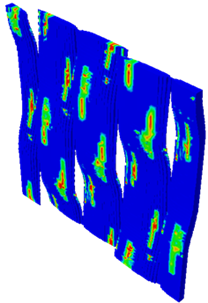
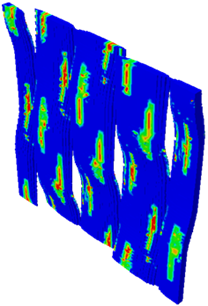
Meso-scale model
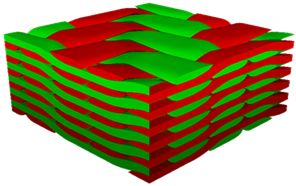
- 3D woven textile, carbon fibre/epoxy, volume fraction ~55%
- Abaqus + periodic boundary conditions + UMAT subroutine
- Results predicted within 10% of experimental values
Experimental and predicted stress-strain curves
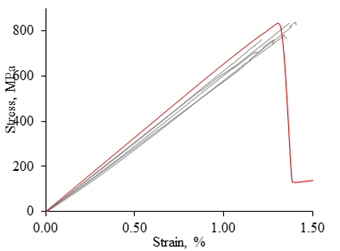
Meso-scale model
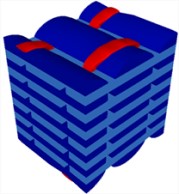
Correct prediction of the fracture surface
SEM image
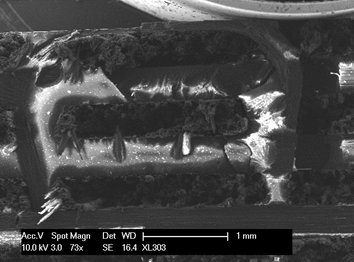
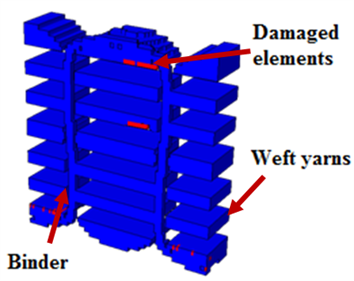
- Idealised meso-model VS realistic model
- 3D woven textile, carbon fibre/epoxy
- Yarn misalignments have a significant effect on properties of the 3D woven composite
Idealised model
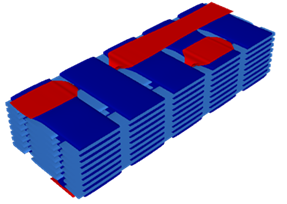
Micro-CT scan
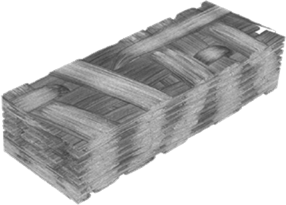
Realistic model
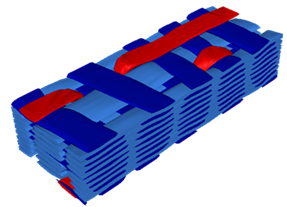