To date, MPE have successfully demonstrated the application of microwave and radio frequency technologies to materials processing at a wide range of scales and TRLs.
The group has a wide portfolio of projects, spanning a range of industries including mining and minerals, energy, polymers and advanced materials, food and bio-products.
Microwave Synthesis of Metal Organic Frameworks
Metal-organic frameworks (MOFs) are highly porous materials consisting of metal nodes connected by organic linkers which have a potential multi-billion pound impact in the adsorbents industry.
Proposed applications of MOFs include, gas capture and storage, hydrocarbon separation, catalysis, wastewater treatment, and innovative healthcare. The potentially high commercial value of MOFs arises from their high porosity and tuneable pore environment which gives them an extremely high capacity and high selectivity for gas and hydrocarbon applications. However, current state of the art in industrial manufacture has restricted widespread adoption of MOFs for commercial applications, as at scale they deliver poor quality materials, whilst incurring high energy and capital costs, meaning that many applications are not economically viable.
Microwave technology can address these challenges through rapid and selective heating, which can increase production rates by orders of magnitude, give controllable product quality and at a reduced energy and potentially capital cost.
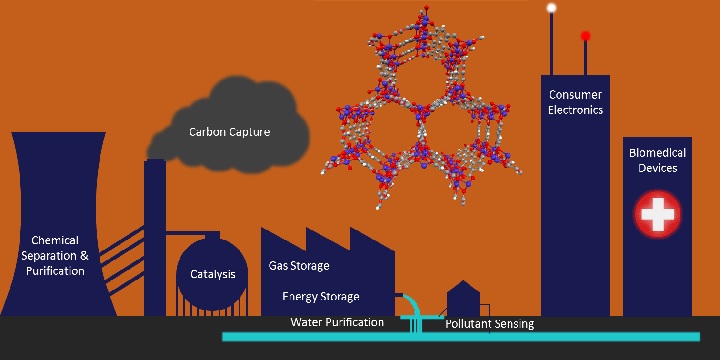
Sustainable Polymer Processing
Information to follow.
Ferrous Bi-Product Recycling using Microwave Technology
Globally, steel making produces approximately 1.5 million tonnes of oily sludge from the hot rolling mill process alone each year. The oil originates from lubricants throughout the process and associated equipment, and traps fine iron particles that cannot be separated from the fluids by physical separation. The sludge is typically landfilled as hazardous waste (at significant cost to producers) or otherwise stockpiled on-site for future handling.
The sludge contains value as a secondary (local) iron and hydrocarbon source, making remediation an attractive option. However, current technology (such as thermal desorption or chemical treatment) to remove the oil to recyclable iron feedstock levels is largely prohibitively energy intensive or otherwise ineffective.
The University of Nottingham, in collaboration with Swansea University (ESRI), Sexton Materials Research Ltd, Darlow Lloyd & Sons, Teledyne e2v and Tata Steel through an Innovate UK project, have trialled the use of microwave technology to remove the oils at laboratory scale. The outcome of the project revealed a significant reduction in de-oiling energy requirements with sufficiently low residual oil content due to selective and rapid heating of the water and ferrous materials contained within the sludge.
The compact, switch-on/switch-off, nature of microwave processing equipment makes it particularly suited to mobile plant operations for remediation of geographically dispersed stockpiled material or as an end-of-pipe process for fresh sludge arisings from the mill. The technical feasibility of the microwave process with hot rolling mill sludge also opens a potential pathway for recycling of other ferrous by-product materials from steel and other industries.
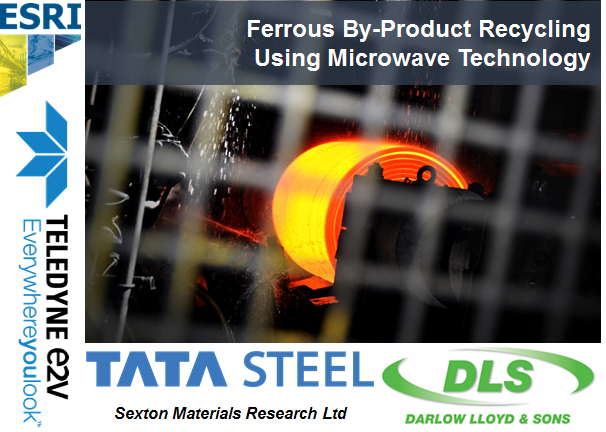
Dielectric Monitoring of Steam Systems
Information to follow.
Microwave IR Sorting of Ores
The growing demand for many mineral commodities combined with a higher embodied energy in their production from falling grades and increased mining activity will place a strain on sustainable mining in the future. The minerals industry has identified ore pre-concentration through the use of sorting technologies as one avenue to help address these challenges by rejecting uneconomic material before it enters the mill, saving on energy expended during comminution and costs associated with fine waste disposal.
Many different methods for excitation and discrimination of valuable minerals exist to form a basis for sorting, including XRF, XRT, NIR, optical, photometric, radiometric and other electromagnetic sensing techniques. The rapid, selective and volumetric heating mechanism provided by microwaves allows for fragments containing valuable minerals to exhibit a temperature rise, while barren fragments containing only rock-forming waste minerals remain unaffected by treatment. This temperature rise can then be measured by infrared thermal imaging.
Working with collaborative and multidisciplinary teams across academia and industry over the last few years, our research has developed a large scale microwave process capable of utilising high power (up to 100kW) and providing high throughputs of up to 100t/h. Our technology has been rigorously tested in a mining environment through pilot plant trials and supported by in-house testing in our laboratory facilities. To date, the project has culminated in one of the world’s largest microwave heating processes and developed significant IP, engineering know-how and fundamental knowledge of microwave processing at large scale and in industrial environments. The project has supported 1 PhD studentship and 5 publications, with several more publications in preparation.
Microwave Assisted Benefication of Ores
The growing demand for many mineral commodities combined with a higher embodied energy in their production from falling grades, finer mineralisation and increased mining activity will place a strain on sustainable mining in the future.
In an effort to address these challenges, minerals industry stakeholders have identified reducing ore competency prior to energy intensive comminution and improving mineral liberation to enable more efficient separation at coarser particle sizes as two important areas of investigation.
High power density microwave treatment has been shown to help achieve these aims through the generation of thermally-induced cracks along mineral grain boundaries leading to preferential breakage and release of valuable minerals. A microwave pre-treatment process could therefore greatly reduce energy consumption in subsequent crushing and grinding stages and help increase valuable mineral recovery in common processes such as froth flotation, gravity/centrifugal separation and/or magnetic separation.
Members of the Microwave Process Engineering group have been developing this application over the last 20 years through a number of collaborative and multidisciplinary projects with some of the world’s largest mining companies and technology specialists. Over the past 5 years, our research and development efforts have taken microwave-assisted beneficiation of ores from small batch laboratory experiments to high power (up to 200kW) and high throughput (up to 150t/h) continuous operation. To date, the project has culminated in one of the world’s largest microwave heating processes and developed significant IP, engineering know-how and fundamental knowledge of microwave processing at large scale and in industrial environments. The project has supported 5 PhD studentships and over 10 publications, with several more publications in preparation.