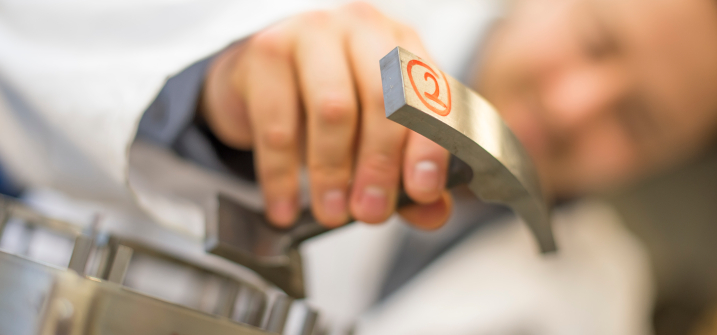
Innovative Fixturing and Tooling
Fixtures and tools are critical manufacturing items in every process as they construct the bridge between the workpiece and the tool that will perform the operation. Because of its importance in manufacturing processes, the MCM is currently researching a number of critical aspects related to jigs and fixtures, focusing both on fundamental research and design of innovative solutions.
Such areas include, but are not limited to, the minimisation of dynamic response during machining operation through passive or active damping, new geometric assembly techniques for improved precision, novel fixturing solutions for high precision components with complex geometries and fundamental research of fixturing of components with non-conventional materials (e.g. composites).
Contacts
Academics
Postgraduates
Research and Development List
Here you can find information about our projects.
Experimental and Numerical Studyof a Fixturing System for Complex Geometry and Low StiffnessComponents
The production of freeform components is challenging, not onlyfrom the point of view of process optimization but also when itcomes to the selection and design of the fixturing systems. Currently,most commercially available fixturing systems are difficultto conform to geometrically complex components; while the systemsthat manage to provide industrially feasible solutions (suchas encapsulation techniques) present several limitations (e.g.,high complexity, limited reliability, and risk of elastic deformationof the part). In this context, the present work proposes a simple,yet efficient, concept of a fixture capable of holding complex componentsthrough the use of compliant/deformable diaphragm elements.
The fundaments of this innovative system (i.e., freeformdiaphragm-based fixturing system) have been simulated throughan experimentally validated finite-element (FE) model, withresults showing a good agreement between numerical and measureddata (displacement average error av¼4.04%). The maininteractions of the system with a workpiece (e.g., contact area andclamping force) have been numerically and experimentally studied,confirming the system’s capacity to generate distributedclamping forces in excess of 1000 N. Based on the modeling activities,an advanced prototype for holding a “generic” freeformcomponent was developed. Using this prototype, a repeatabilitystudy then showed the capacity of the system to deterministicallyposition and hold complex geometries.
Finally, the proposed fixturingsystem was thoroughly evaluated under demandingmachining conditions (i.e., grinding), and the results showed theability of the fixture to maintain small part displacement(dx<10 lm) when high cutting forces are applied (Max.FR¼1021.24 N). Design limitations were observed during thegrinding experiments, and the lineaments are presented in orderto develop improved further prototypes. Overall, the proposed fixturingapproach proved to be a novel and attractive industrialsolution for the challenges of locating/holding complex componentsduring manufacture.
Tell me more
A solution for minimising vibrations in milling of thin walled casing by applying dampers to workpiece surface
Milling of large thin walled casings with complex features needs appropriate damping solutions toachieve required workpiece surface quality when utilising aggressive machining parameters. In thispaper a novel surface damping solution composed of a thin flexible layer mounted with distributeddiscrete masses attached with viscoelastic layer is presented. Damping of higher frequencies through aflexible layer and subsequent lower frequencies through added masses enables damping over a widebandwidth. Finite element modelling and validation of the proposed solution showed a significantdamping of workpiece and corresponding reduction in machining vibration by more than four times.
Tell me more
Coupled interaction of dynamic responses of tool and workpiece in thin wallmilling
Chatter free thin wall machining requires knowledge of the dynamics of a machine-tool system and workpiece either for designing damping solutions or for modelling impact dynamics. Previous studies on thin wall milling mostly focussed on stability studies. However studies on the interaction between the tool and workpiece responses in thin wall machining are scarce in the literature. In this work, the coupled dynamic response of tool and workpiece is presented both for an open (thin wall straight cantilever) and for closed (thin wall ring type casing) geometry structures.
Experiments were carried out for different tool overhangs and depths of cut and the machining vibration signal was analysed in time–frequency domain to study the interaction, i.e. coupling, of tool–workpiece dynamic response at various cutting tooth engagement/idle times. The findings from this study highlight the importance of tool's frequency, particularly torsional and first bending modes, in impact dynamics of thin wall milling.
Moreover, the differences in dynamic response interaction between a cutting tool and thin wall plate and a cylinder are identified. While the analysis of the open geometry structure showed the presence of tool and workpiece responses for any depth of cut, results on closed geometry structure exhibited a complete dominance of tool mode at higher depths of cut. These findings are of critical importance in understanding the impact dynamics in thin wall milling and also of effectiveness of passive damping solutions.
Tell me more
An assessment of “variation conscious” precision fixturing methodologies for the control of circularity within large multi-segment annular assemblies
The fixturing of large segmented-ring assemblies is of importance to a number of key high value industries such as the aerospace and power generation sectors. This study examines methods of optimising the circularity of segmented-ring assemblies, and how the manufacturing variation within each element (i.e. segment wedge) contributes to overall assembly variability. This has lead to the definition of two original assembly methodologies that aim to optimise an assembly, so that circularity errors are minimised for a given set of components.
The assembly methods considered during this study include a radial Translation Build (TB) and a Circumscribed Geometric (CG) approach, both of which are compared to a traditional Fixed Datum (FD) build method. The effects of angular, radial, parallelism/flatness and chord length variability within the component geometry, and their effect on the circularity of the final annular assembly are examined mathematically and experimentally.
Furthermore, the inherent loss of assembly circularity due to differences between component and assembly sagitta is also considered, along with the stepping caused by dissimilar adjacent component radii as a result of manufacturing variation. Experimental results show that the CG build method offers a significant improvement in circularity in most situations over the benchmark FD build method. This contrasts the TB results that proved to be the least consistent in terms of circularity, but better in the control of angular breaking errors within the assembly.
Tell me more
Assessment of adhesive fixture system under static and dynamic loading conditions
Adhesive fixture systems have several advantages over conventional fixturing methods due to the following key capabilities:(1) can hold components with increased workpiece accessibility for processing, (2) can hold delicate componentswhile avoiding excessive clamping forces, and (3) can hold and support complex or variable geometry parts.
The developmentof high-strength structural adhesives that can be rapidly and controllably cured now offers much greater scopefor holding complex parts than the traditionally used low-strength adhesives, waxes, or low-melt alloys currently used inniche applications and ad hoc fixture systems. This article first evaluates the workholding performance, capability, andsuitability of an ultraviolet-activated adhesive fixture system to hold aerospace-type components; this includes quantifyingthe mechanical properties of the adhesive bond and assessing the influential factors (surface finish, contamination, geometriesof bonded surfaces, and adhesive-curing time).
Then the article presents concepts of adhesive fixture system forrapid location and bonding/de-bonding for enhanced accessibility on machine surfaces. A set of fixture demonstratorsand their effectiveness are evaluated in terms of maximum reaction forces, dynamic performance, and ease of use. Fromthis research, it becomes apparent that the adhesive fixture system approach provides new opportunities for workholdinggeometrically complex components for high-demanding applications (e.g. manufacture of aerospace parts).
Tell me more