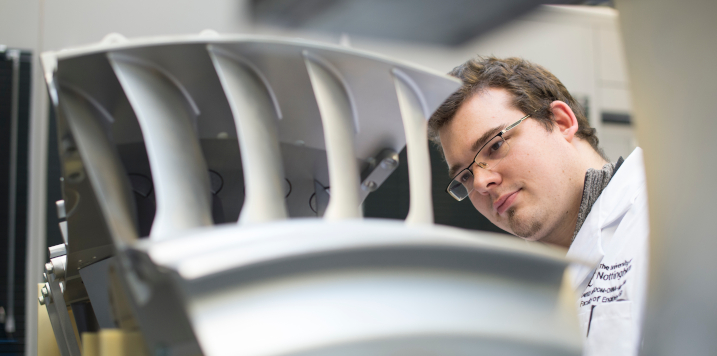
Closed Projects
Collaboration with industrial partners and universities (UK & Europe) throughout the years has led to the establishment of the MCM group as a high profile research team. Numerous successful projects have been completed in the field of advanced machining (energy beam processing, diamond and ultra-hard compounds, bone cutting, etc.), and multidisciplinary projects related to robotics and repair of high value industrial installations (e.g. aeroengines).
Funded projects
INSPECT (In-situ optical inspection of engine components)
With the civil aviation sector continuing to grow year-on-year, an ever increasing number of routine in-situ gas turbine inspections are undertaken by both gas turbine providers and their customers. Whilst these are critical for ensuring a high-level of aeroengine safety, they are time intensive, vary between inspectors, and offer limited data capture and assessment possibilities. Through the INSPECT consortium, an optical inspection system will be developed that can be permanently and retrofittably embedded into the gas turbine borescope ports. Upon engine shutdown, probes are automatically inserted into the engine gas path, providing an fast, frequent, and standardised compressor inspection after every operation. INSPECT is a state-of-the-art inspection technology, enabling future Big Data Analytics, data mining, and trending. This will ultimately make RollsRoyce and its customers data rich and able to optimise flight paths, maintenance schedules, and possibly even OEM design.
Tell me more
Participant organization names:
Funder: Innovate UK
COBRA (Continuum Robot for Remote Applications)
Imagine if an engineer could inspect and repair a pipe deep within a nuclear reactor without having to get changed into a HAZMAT suit, or even perform an inspection and then repair a jet engine still attached to the wing of an aircraft, but from the comfort of their own home. COBRA (Continuum Robot for Remote Applications) aims to do just that. A consortium of industrial companies and academic institutions aims to design, develop and build a novel solution for remotely controlled specialist robots that will enable maintenance & repair tasks to be undertaken in extreme environments by teleoperation without compromising the health and safety of the operators.
COBRA will reduce lifecycle costs, provide rapid worldwide operational response to issues, and improve the safety and quality of high value installed infrastructures. The continuum robot (a.k.a. snake robot), will be long enough to be deployed in a range of pipe based nuclear fission and fusion scenarios, as well as small enough in diameter to be applicable to jet engine deployment through conventional inspection ports. The main objectives of COBRA include production of a full scale teleoperated prototype, inclusive of the control software, a range of shape sensors and two separate, interchangeable and innovative 'end effectors'. Firstly, a 3D camera to provide high resolution views of the environment and feed into an immersive interface with augmented reality elements. Secondly, a miniature laser processing head to allow robotic corrective action to take place. A miniature laser head has been developed by OpTek Systems Ltd for a specific application in Rolls-Royce Aerospace, but COBRA will develop the miniature laser control head to work in challenging new environments opening new markets for OpTek to exploit.
Tell me more
Participant organization names:
Funder: Innovate UK
RAIN (Robotics and Artificial Intelligence for Nuclear)
The nuclear industry has some of the most extreme environments in the world, with radiation levels and extremely harsh conditions restraining human access to many facilities.
Yet to date, robotic systems have had very little impact on the industry, even though it is clear that they offer major opportunities for improving productivity and significantly reducing risks to human health.
The RAIN initiative has been created to address these issues by developing the advanced robotics and artificial intelligence that will be essential for future nuclear operations. Their adoption will have the potential to completely transform the nuclear industry globally.
At the same time it is envisaged that the reliable, functional robotic systems that are the programme’s goal will also have important applications in other sectors. These will extend beyond extreme environments such as space exploration, in-orbit satellite design, offshore operations and mining to include less challenging areas where RAIN research will be highly relevant, such as healthcare and autonomous vehicles.
The programme’s overall objectives are to lower costs within the nuclear industry, reduce timescales, reduce risk, improve safety, promote remote inspection and reduce the chances of human exposure to radiation and other hazards. Once developed, the technologies that will help to realise these objectives are to form the foundation of a world-leading robotic and AI research and innovation ecosystem.
Tell me more
Participant organization names:
Funder: EPSRC
STIMULANT (Surface integrity conscious high-performance hybrid machining for safety-critical superalloy aeroengine parts)
STIMULANT aims to develop and demonstrate “surface integrity conscious” hybridisation of machining processes for safety-critical aeroengine parts that is able to deliver a step-change in Material Removal Rates (MRR) and reduction in production costs. STIMULANT will take key knowledge at different levels of maturity that exists within Consortium, and progress it, via Standard Features (StdFs) methodology, to the demonstration on “engine-like” safety-critical parts.
Tell me more
Participant organization names:
Funder: Clean Sky 2 - Horizon 20-20
FLARE (Flame Spray Adder for in-situ Patch Repair of Aero-Engine Combustors)
ATI-approved project Flame Spray Adder for in-situ Patch Repair of Aero-Engine Combustors (FLARE), led by Rolls-Royce is a collaborative R&D project utilising continuum robot capability developed by the University of Nottingham, incorporating miniaturised flame spray equipment from Metallisation. There is significant market desire to create a device that can perform in-situ / on-wing patch repair of thermal barrier coatings without dismantling high value infrastructure, such as aircraft jet engines.
It is costly and time consuming for maintenance and overhaul activities to be completed whilst the engine is removed, it is more attractive to Rolls-Royce, airline customers and the aerospace sector’s supply chain to be able to perform more services with the engine still intact and attached to the aircraft.
Tell me more
Participant organization names:
Funder: Innovate UK
REINER
Aeroengine compressor blades are sometimes damaged by ingested debris. Damaged blades can currently be repaired by highly-skilled Rolls-Royce engineers that travel to the location of the engine to remove the defect using slender grinding tools, an operation known as boreblending. Remote Inspection and Engine Repair is a project that aims to develop a portable, remotely controllable boreblending robot. Led by Rolls-Royce and funded by the ATI, the project aims to reduce the downtime associated with boreblending by allowing engineers to perform the task remotely over the internet.
The remote boreblending robot was demonstrated on a Trent XWB engine in Rolls-Royce, Derby, in January 2018.
Participant organization names:
Funbder: Innovate UK and Aerospace Technology Institute
DIROBONE
This project is focused on the development of a process for the fabrication of personalised intervertebral spine implants using robotic technology and bone tissue; in order to achieve full biocompatibility in the treatment of spine injuries and chronic degenerative diseases.
The outcomes include intellectual property application, a dissemination strategy for the academic results, the enhancement of the scientific and innovative competencies of students and researchers in both sides of the collaboration and the improvement of a mutual research line dedicated to the development of medical devices for developing countries.
Tell me more
Participant organization names:
Funder: British Council - CONACYT
STEEP (Synergetic Training network on Energy Beam Processing: from modelling to industrial applications)
The STEEP project is a Marie Curie Initial Training Network aimed to develop researchers in field of energy beam processing (pulsed laser ablation, abrasive waterjet and focussed ion beam). This involves both multi-disciplinary scientific training, secondments in both academia and industry and tailored courses in complementary skills.
The overall aim of the STEEP Initial Training Network is to establish a transnational research and training platform for the formation and career development of young researchers on energy beam (EB) processing methods - laser, abrasive waterjet machining and focused ion beam machining - which together represent a scientific field of critical importance for further advancement of European of high value-added manufacturing industry.
Whilst these processes differ in nature, a set of key commonalities can be identified among them when considered as dwell-time dependent processes; this allows the approach of EB processes under a unitary technology umbrella. The key element that brings all the EB processing methods together under the STEEP umbrella is a unifying modelling platform of the footprints, as a result of energy beam - workpiece interactions, followed by the development of an original beam path simulator.
Tell me more
Participant organization names:
Funder: European Comission
MiRoR (Miniaturised Robotic systems for holistic in-situ Repair and maintenance works in restrained and hazardous environments)
MiRoR (Miniaturised Robotic systems for holistic in-situ Repair and maintenance works in restrained and hazardous environments) aims to develop a novel concept of a Miniaturised Robotic Machine (Mini-RoboMach) system that will be demonstrated for holistic in-situ repair and maintenance of large and intricate installations.
Tell me more
Participant organization names:
Funder: European Comission
Tell me more
DIPLAT (Enabling advanced functionalities of Diamond and other ultra-hard materials by Integrated Pulsed Laser Ablation Technologies)
Diamond and other ultra-hard materials (e.g. cubic boron nitride) possess outstanding mechanical, wear and thermal properties that make them attractive to manufacture a wide range of high value-added products such as high-performance, smart tooling. However, due to the extreme properties of this group of materials, efficient and precise generation of complex 3D freeform geometries and structures to meet the needs for further development of high-performance tools is still a challenge.
DIPLAT addresses the need for an efficient, precise and flexible processing technology for ultra-hard materials in tooling applications, in order to fully exploit the potential of these materials. By smartly utilizing the developments of high brilliance short and ultra-short pulsed lasers, a tooling technology based on 3D Pulsed Laser Ablation (PLA) will be developed and demonstrated for various industrial applications. DIPLAT will introduce whole new technology platform for producing ultra-hard tools with enhanced functionality, outstanding machining performance and superior lift-time.
Tell me more
Participant organization names:
Funder: EU FP7
Tell me more
ConforM-Jet
Innovative control philosophies that enhance the capabilities of niche processing methods are of critical importance for EU manufacturers of high value added products made of advanced engineered materials.
High Energy Fluid Jets (HEFJet) processing is a niche technology with outstanding capabilities: cuts any material at negligible cutting forces; generates virtual zero heat; uses the abrasive jet plume as a “universal tool”. Nevertheless, freeform machining by High Energy Fluid Jets Milling (HEFJet_Mill) is still at infancy level. This is because no control solution for HEFJet_Mill exists.
ConforM-Jet has developed and demonstrated, for the first time, a self-learning control system for HEFJet_Mill to generate freeform parts. This has been done by integrating models of HEFJet_Mill with patterns of multi-sensory signals to control the outcomes of jet plume – workpiece interaction, i.e. magnitude and shape of abraded footprint; these are key issues in controlling the generation of freeforms via HEFJet_Mill.
Tell me more
Participant organization names:
Funder: EU FP7
Student projects
Closed Projects List
Project Title | Year |
Damage assessment of cortical bone and a novel setup to mimic its in-vivo conditions during machining
Student's name: Jose Robles
|
2022
|
Wearable EyeGlove System for Measurement and Localization in Confined Environments
Student's name: Erhui Sun
|
2022
|
Design and Modelling of a Reconfigurable Parallel Kinematic Machine with Customisable Leg Layout for Enhanced Performance.
Student's name: Josue Camacho
|
2021
|
Novel approach for grinding SiC-based ceramic matrix composites (CMCs)
Student's name: Gonzalo Garcia
|
2021
|
Towards the understanding of the transient behaviour and sources of variability on the process outcomes in inertia friction welding
Student's name: Luca Raimondi
|
2020
|
Surface Texturing on Dry-Lubricated Transmissions and Power Systems to Deliver Better Performance and Simplified Systems in Aerospace Engineering
Student's name: Liang Ding
|
2020
|
Toward understanding of laser beam interaction with advanced materials
Student's name: David Cha
|
2020
|
Novel Systems for Position and ForceControl of Slender and Compliant Robotsfor In-Situ Machining.
Student's name: David Alatorre
|
2020
|
An investigation into the thermal management and control of ceramic injection moulding die-tools.
Student's name: Floriana Bianchi
|
2019
|
Machinability and surface integrity investigation of materials based on energy thresholds investigation and innovative pendulum based machining.
Student's name: Dongdong Xu
|
2019
|
Towards improvement of linear friction welding through innovative design and simulation of tooling and fixturing systems.
Student's name: Dorian Lachowicz
|
2019
|
On understanding the materialremoval mechanism when cuttingCeramic Matrix Composites (CMCs).
Student's name: Oriol Gavalda Diaz
|
2018
|
On Modelling and experimentation of planar grinding using abrasive pads with grits of defined geometries and distributions for enabling controlled surface texture.
Student's name: Yuchen Zhou
|
2018
|
Conformable fixture systems with flexure pins for improved workpiece holding.
Student's name: Oliver Craig
|
2018
|
Dressing tools with controlled abrasive grain population for grinding aerospace materials.
Student's name: Alessio Spampinato
|
2018
|
Investigation of combustion flame spray as in-situ repair technology for thermal barrier coatings.
Student's name: Francesco Fanicchia
|
2018
|
Self Calibration Method for a Portable Parallel Kinematic Machine Tool.
Student's name: Aitor Olarra
|
2018
|
Fabrication of Nanomaterial-impregnated vitrified CBN grinding wheel in strong magnetic field and wheel grinding.
Student's name: Li Haonan
|
2017
|
Resaerch on bone cutting and a novel tool development.
Student's name: Zhirong Liao
|
2017
|
Laser process optimisation for in-situ repair of aero-engine components.
Student's name: David Gilbert
|
2017
|
Method for in-situ balancing of rotatives by use of an on-the-fly pulsating material removal process.
Student's name: Moritz Carl Stoesslein
|
2016
|
Variation conscious assembly fixturing methodologies for the preliminary weld proceesses of segmented ring structures.
Student's name: Stewart Lowth
|
2016
|
Stochastic modelling of abrasive waterjet controlled-depth machining.
Student's name: Pablo Lozano Torrubia
|
2016
|
Control of navigation and feeding actions of a continuum arm for in-situ repair.
Student's name: David Palmer
|
2016
|
Numerigal and experimental study of an innovative fixturing system for components with complex geometries.
Student's name: Andres Gameros
|
2016
|
Design of contiuum robot for in-situ repair of aero engine.
Student's name: Xin Dong
|
2015
|
An analysis of a walking parallel kinematic machine tool.
Student's name: Adam Rushworth
|
2015
|
On design and simulation of passive damping solutions for milling of thin-walled parts.
Student's name: Kiran Kolluru
|
2014
|
Pulsed laser ablation(PLA) of ultra-hard structures: Generation of damage-tolerant freeform surfaces for advanced machining application.
Student's name: Manuela Pacella
|
2014
|
Influence of anomalies from hole drilling operations on fatigue performance for a nickel-based superalloy in aeroengine disc application.
Student's name: Chris Herbert
|
2013
|
Modelling of Abrasive waterjet milled footprints.
Student's name: Saqib Anwar
|
2013
|
Solid diamond micro-abrasive tools cenerated by energy beam ablation.
Student's name: Paul Buttler-Smith
|
2012
|
Development of a miniature low forge machining system for in-situ maintenange.
Student's name: John Allen
|
2011
|
Response of special purpose aerospace materials to abrasive waterjet machining
Student's name: Carol Kong
|
2010
|
The development of a manufacturabilty analysis system for micro-milling
Student's name: Syaimak Abdul Ahukor
|
2010
|
On understanding the mechanisms affecting surface integrity during hole making operations on an advanced Ni-based superalloy.
Student's name: Julian Marinescu
|
2009
|
Investigation of monitoring techniques for the detection of tool/workpiece malfunctions in milling of heat resistant alloys.
Student's name: Jacky King Chung Jwong
|
2009
|