ACEL Projects
Here you can find information about currently active projects.
Processing of non-conductive aerospace materials by EDM
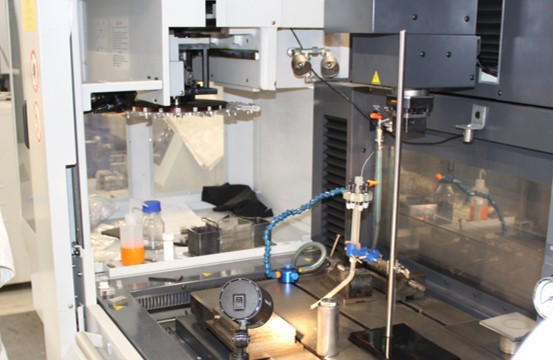
Overview
This project investigates the machining of ceramic and non-conductive materials through Electrical Discharge Machining (EDM). The main drive behind this research is the currently high demand in micro-machining parts inside industries such as automotive and aerospace, hence, the need of investigating and expanding the EDM capabilities to non-conductive aerospace materials.
On a parallel side, it is also being investigated the potential use of viscous dielectrics for EDM. With this, its being carried out experimental procedure on different types of viscous dielectrics and how they contribute with the improvement of the process.
Investigation in EDM of aerospace components
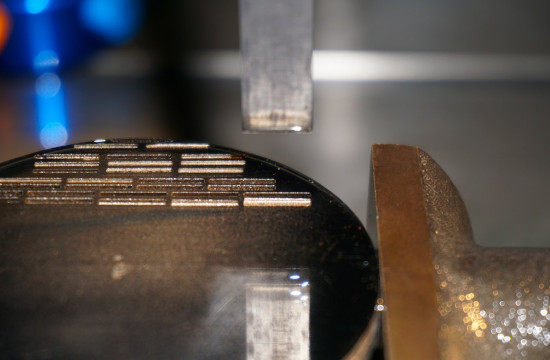
Overview
I am currently working on 3 projects revolving around improvement and innovation of EDM in aerospace component processing.
Oxides in EDM are unwanted as they decrease the integrity of the EDM surface as well as causing problems further on in the manufacturing process. I am currently undergoing a fundamental investigation of oxides in EDM recast layers with the aim of improved EDM surface processing by reduction of unwanted surface features.
Graphite electrodes are the most common electrode however not much is explored concerning the influence of structure. I am researching the influence of electrode structure on electrode properties, wear, and material removal mechanisms, and the compound influence on EDM in terms of the recast layer and machining characteristics.
I am investigating the influence of dielectric structure on dielectric properties and thus forming alternative dielectrics with tailored physical properties for niche applications in EDM.
Study on the formation mechanism of electrical discharge coatings
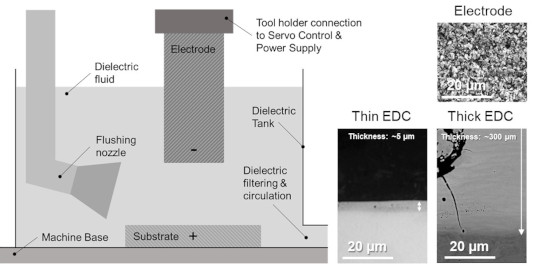
Overview
In Electrical Discharge Machining (EDM), pulsed electrical discharges between an electrode and workpiece, submerged in a dielectric fluid allow for the machining of an electrically conductive workpiece. Electrical Discharge Coating (EDC) is a variant of the EDM process whereby material from a sacrificial electrode is transferred through a dielectric fluid to form a coating on the workpiece. The technology can be classified under Thin or Thick EDC. In this project, an investigation into the effects of coating parameters on coating properties is carried out to elucidate the fundamental mechanism by which the coatings are produced.
Additive Manufacturing In-Space
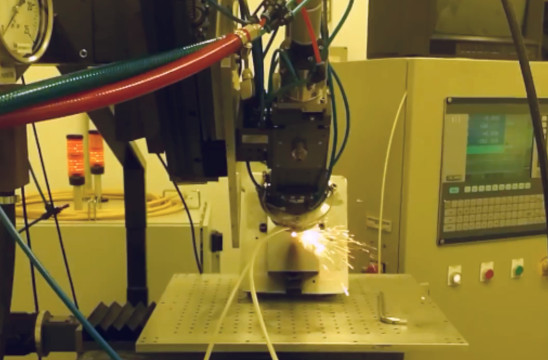
Overview
Laser Directed Energy Deposition (DED) is an additive manufacturing process where parts are built by blowing metal powder into a laser beam to melt powder into tracks and then layers, generating components. In this project, magnetic fields are being used to refocus the powder, to change and improve how this powder is deposited. This includes reducing powder wastage, modifying the shape of tracks, and making the process more reliable, potentially allowing it to be used in challenging environments, such as space.
Electron beam processing for the smoothing, doping and modification of PVD-AM coating-substrate systems
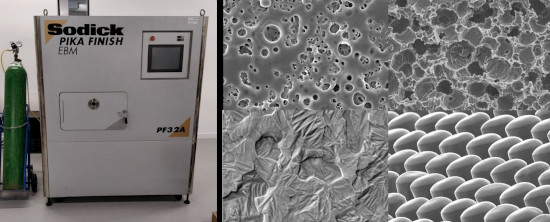
Overview
Research into the use of Low Energy High-Current Electron beams (LHEBs) for the modification of materials is well established. This project has identified the need for a next-generation surface treatment technology for modifying the rough, complex textures found in Additively Manufactured (AM) as-built Selectively Laser Melted (SLM) material. This is an exciting opportunity to combine these technologies, in conjunction with additional doping of the surface via direct attachment and novel electron beam modified thin film coatings.
Microstructural control for next generation additive manufacturing
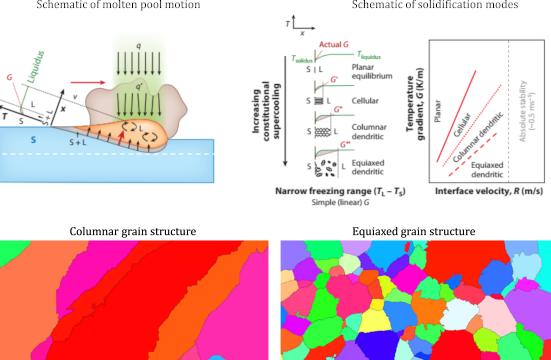
Overview
Selective laser melting (SLM) is an additive manufacturing technology utilizing a laser beam to melt powder materials together layer-by-layer for 3-dimensional part fabrication. Due to its superior rapid prototyping capability of complex structures, SLM has been widely accepted for industrial applications including aerospace, automotive, and medical devices. However, a more comprehensive understanding on the process-microstructure-properties correlation has not yet been revealed. The metallic additive manufacturing process comprises of non-uniform temperature gradient and rapid thermal cycles that leads to microstructures with porosity and anisotropy, drastically different from their cast or wrought counterparts. Such different microstructural features critically affect the mechanical properties of the additively manufactured parts. Therefore, understanding of microstructure evolution during SLM is crucial to achieve improved process control and provide the performance of laser-fabricated components. This project aims to control the microstructure of Ti-6Al-4V alloys for the next generation additive manufacturing.
Effect of powder feedstock on processing of alloys by laser powder bed fusion (LPBF)
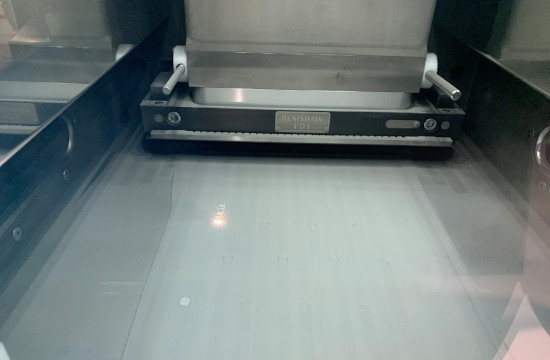
Overview
The main aims of this project are to study the effects of powder feedstock on the properties of final LPBF parts. There are some aspects that need to be considered for powder feedstock, with particle size distribution and chemical composition being the most important factors as they can influence almost all other powder properties and play a crucial role in final parts properties. Therefore, studies will be carried out to get an understanding of how particle size distribution and chemical composition affecting the powder feedstock performance and final parts performance with the full consideration of processing parameters. Finally, perfect powder feedstock for LPBF technique is expected.
Processing of WC-Co by DLD and SLM
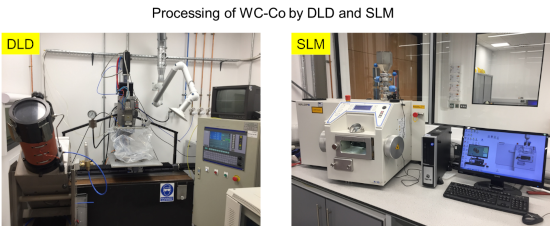
Overview
This research investigates the processability of a satellited WC-Co composite powder in direct laser deposition (DLD) and selective laser melting (SLM) technologies. The WC-Co is widely used as a protective material for many wear resistant applications such as cutting tools. The employment of additive manufacturing can help to increase design flexibility, reduce the time of manufacturing, and increase material efficiency.
Re-using machining chips: towards zero carbon manufacturing
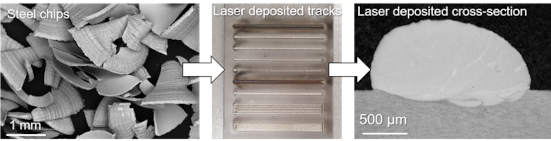
Overview
Iron and steel production accounts for 9% and aluminium for 1.5% of global process and energy CO2 emissions. The critical manufacturing process of machining generates significant levels of machining chips which are either discarded or recycled, which still generates substantial levels of CO2. This project investigates the use of machining chips as a substitute feedstock material for laser and solid state manufacturing.
Laser ultrasound for monitoring in additive manufacturing
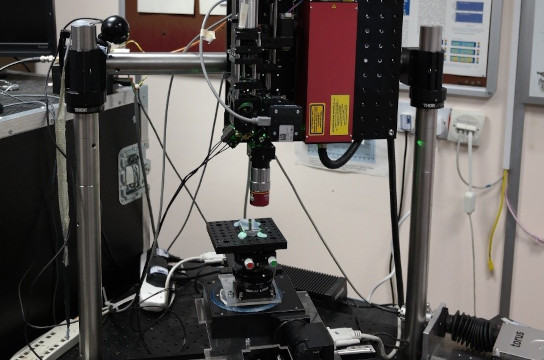
Primary Supervisor
Prof Matt Clark
Overview
Additive manufacturing (AM) offers a paradigm shift in engineering as previous design constraints, such as tooling paths in machining, are removed. The ability to create novel free form structures, such as lattices, clearly offers vast potential benefits for high performance industries including aerospace, medical and tooling. Combined with the ability to alloy in-situ and numerous post-processing routes, the variety of final parts in AM is almost unlimited and not yet well understood. This necessitates a tool for inspection and qualification of AM specimens.
The ability to probe the materials surface acoustic wave (SAW) velocity, and hence the underlying microstructure, at previously unfeasible speeds and areas of acquisition makes laser ultrasound a good candidate for monitoring and qualification in AM.
An example of two works of the project is 1. To study and correlate the rolling force in Wire-Arc AM with the resulting final microstructure. 2. Perform inversions on the SAW velocity to measure the elastic properties of the AM specimens, particularly useful in novel alloys.
Creep behaviour of LPBF alloy 718
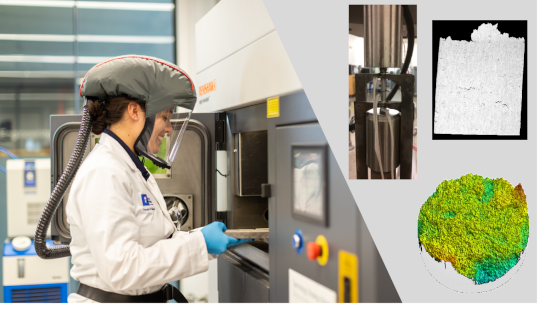
Overview
Components manufactured by laser powder bed fabrication (LPBF) are fundamentally limited by their performance for use in critical applications. With respect to high temperature materials produced via LPBF, microstructural defects - such as unfavourable precipitate formation, suboptimal grain size and distribution - and macroscale anomalies - like lack of fusion, intra/inter layer defects - often result in LPBF components performing well below their wrought counterparts. Little research has been conducted on the creep performance of LPBF materials.
Hence, this work investigates the creep performance of alloy 718 parts, fabricated with different scanning strategies, build orientations, and numbers of laser per parts. Microscopy and Fractography are being conducted for this project. Staged and Interrupted creep tests are also performed to further understand the creep phenomena in Additively Manufactured (AM) materials. Finally, creep modelling for AM materials is also conducted.
High cycle fatigue analysis of SLM-processed nickel-superalloy inconel 718
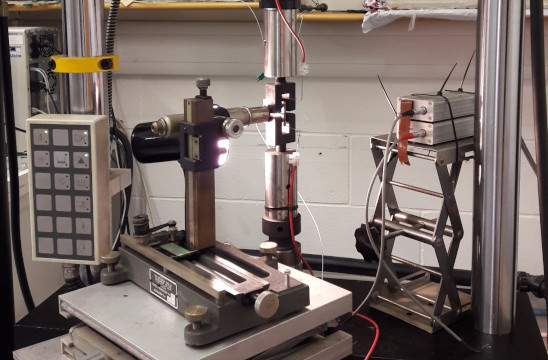
Overview
Inconel 718, a nickel-based superalloy is most commonly used in the aerospace industry due to their superior mechanical performance. Of the many reasons for metal failure like corrosion, stress concentration, temperature and overload, fatigue is one of the root causes. This research aims to study the fatigue behavior of the aforementioned alloy manufactured through powder-bed fusion, analyse and limit the fatigue crack growth. High cycle fatigue tests are performed on compact-tension specimens at 20Hz with a stress ratio of 0.1 at room temperature.
Improving production rate in Laser Powder Bed Fusion (LPBF)
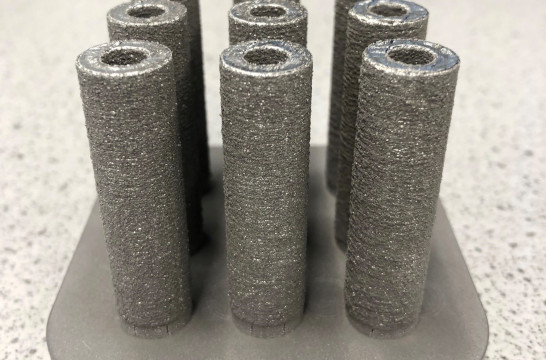
Overview
The time taken between the conception of a part and the realisation of a part in Additive Manufacturing is far quicker than traditional manufacturing techniques such as die casting, since the only prerequisites to printing are digital (CAD file, build file). However, when considering only the machine time to produce a single part, AM techniques like Powder Bed Fusion exhibit build times to the order of hours/days, as opposed to wrought techniques that likely take seconds/minutes. This research aims to improve the production rate of laser PBF by investigating the use of larger layer thicknesses, and mitigating penalties to part quality through manipulation of feedstock properties and further understanding of defect mechanisms.